Multi Tie Tamper : Ballast Compaction Railroad Facility
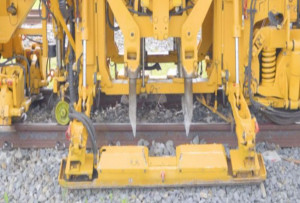
Grobogan – the Railway Maintenance Center manages various railway facilities, one of which is the Multi Tie Tamper (MTT) special equipment. There are thirteen MTT facilities that are under the care of the Railway Maintenance Center, which are spread over five provinces in Indonesia, including North Sumatra, South Sumatra, West Java, Central Java, and South Sulawesi.
Multi Tie Tamper is a means of transportation that is rarely seen on railroads. So that people are rarely familiar with this facility, including rarely knowing the use of the facilities which are generally yellow.
In general, MTT or called tamping machine is one type of heavy machine that is very important in the field of rail road maintenance. MTT functions to compact the stones under the ballast / kricak. The ballast under the bearing will be compacted by the tamping unit in the MTT.
Today's train is increasingly becoming the prima donna of transportation for the community. The increasing rail traffic, along with the passage of time (in this case closely related to the operation of the rail line), the construction of railroads is subjected to loads from a series of trains that pass on it repeatedly and is always related to the weather. This resulted in four impacts, firstly the wear of the rails caused by the lateral and longitudinal trajectory forces or by braking forces, the second damage to the rail fastening equipment and bearings, the third decrease in the function of the ballast due to internal and external contamination processes, and four damage to the subgrade due to the entry of stones. ballast due to carriage load.
Of all the factors mentioned above, the most dominant or easily damaged are ballast and subgrade. This is because the load received by the ballast and subgrade is a dynamic load that works regularly/periodically during the service life. And ballast is a loose material where in the field quality/strength control is rather difficult. While the subgrade in each location the strength of its carrying capacity (CBR value) varies, and generally during the rainy season will experience a decrease in its carrying capacity.
As for rails and bearings, especially concrete and steel bearings, the level of damage is relatively small. This is because the quality uniformity of concrete/steel rails and bearings is easy to obtain because the concrete/steel rails and bearings are made in the factory (fabrication).
Railroad construction serves to serve the flow of train traffic comfortably. Comfort is closely related to the feeling received by passengers who board the train, where there is less shock and noise from the train.
To keep the condition of the rail road in good condition, it is necessary to hold ballast compaction regularly. Compaction work is carried out regularly whose method is adjusted to the planned schedule, with several methods, namely, first manually, for manual compaction, the frequency of compaction is carried out every 2 (two) months in the same area. Second, the Mechanical Method Using a Light Pecok Machine, for compaction using a Light Pecok Machine, the frequency of compaction is carried out every 6 (six) months in the same area. Third, the Mechanical Method Using a Heavy Beat Machine. For compaction using a heavy crushing machine, the frequency of compaction is carried out every 2 (two) years in the same area.
With regular compaction, it is hoped that the construction life will be longer and create a safe and comfortable atmosphere for rail road service users.
Mechanical Method Using Heavy Beat Machine. Compaction with a Heavy Beater Machine uses a motorized carriage with a generator and machines to move the ballast compactors, this tool is called the Multi Tie Tamper (HTT).
The matching of the ballast under the bearing is carried out automatically by vibrating and pressing. Where this pemecokan is done without ballast scraping first.
The selection of the area to be beaten takes into account several factors, a) The beating with heavy atesin must be carried out in a fairly long area, not in a short area, where for a short area a light pounding machine (HTT) can be used. Then, b) Heavy machine punching gives the best possible result in terms of quality and durability.
Matching using a machine in this case is a Multi Tie Tamper railway facility will get optimal results if the following specified requirements are met: first, the layer under the ballast (sub ballast) is in good condition, second, the ballast is in clean condition, third, the rail material (rails and bearings) must be in good condition, fastening devices are properly locked and joints are well maintained.
The workability of Multi Tie Tamper is greatly influenced by the condition of rail traffic. This is because the existing rail road in Indonesia is single track (Single Track), so Multi Tie Tamper cannot work optimally.
Tamping units on the MTT are controlled through a control room run by a special operator in the facility. The depth of punching can be adjusted through the control cabin with units of mm, which of course makes it more precise. In addition to being beaten, the existing rails will also be lifted, meaning that the bearings under the rails can be compacted with ballast stones.
Before carrying out ballast compaction, it is necessary to know in advance the train traffic that has a long period of time between one train and another. Under normal conditions, the Multi Tie Tamper working ability is + 250 - 500 meters/hour.
The magnitude of the shock and noise of the train is greatly influenced by the ballast spring, the train spring system and the train speed. Ballast spring is strongly influenced by ballast conditions, where if the ballast is dirty then the ballast spring is reduced which has a very large impact. (yogo)
Zulkarnain, Yanra, Ghofarudin. 1995. The Process of Washing and Compacting Ballasts on the Yogyakarta-Solo Railroad. Final Project of the Islamic University of Indonesia, Yogyakarta.
Komentar
LOGIN FOR COMMENT Sign in with Google